Consul
InterNACHI Narrative Library for Microsoft Word/Excel
InterNACHI Narrative Library for Microsoft Word/Excel
Couldn't load pickup availability
This product is a digital download. You will not be physically shipped any products.
You must have Microsoft Word and/or Excel installed to use this Library!
All content Copyright 2023, by Kenton Shepard, CMI About the author
7,800 narratives you'll never have to write... we've done it for you!
THE LIBRARY
The InterNACHI Narrative Library is a huge collection of home inspection narratives. With over 2,200 unique headings and subheadings it dwarfs any other narrative library available anywhere.
The Library is available as a series of folders organized by home system. The MS Word documents contain narratives that can be copied and pasted into any inspection software regardless of file format.
ONBOARD REFERENCE MATERIAL
The library also includes 40,000+ words of reference material, including:
- Inspection checklists;
- System descriptions, explanations and regulations;
- HVAC date codes;
- Links to online manuals;
- Lists of educational resources;
- Articles on:
- Inspection approaches;
- Report writing;
- Systems and components;
- Using photos/videos, and much more!
Reference material is accessible any time the template is open.
SPECIALTY REFERENCE and NARRATIVES
This template also includes comprehensive sections on:
- Log Homes (100 headings/subheadings);
- Pool & Spa (75 headings/subheadings);
- Thermal Imaging (17 headings/subheadings); and
- Commercial roofing (115 headings/subheadings: EPDM, Built-up, TPO. PVC).
SUPPORT
For questions about this template, please contact Kenton: kenton@internachi.org 720-646-8724
Also available in other versions here
OTHER WRITTEN WORKS BY KENTON SHEPARD
Home Inspection Report Writing Guide (PDF)
Log Home Inspection Checklist (PDF)
Expert Witness Contract Template (PDF)
FIELD GUIDES BY KENTON SHEPARD
InterNACHI Asphalt Shingle Defect Recognition Guide (PDF)
InterNACHI Field Guide for the Inspection of Tile Roofs (PDF)
InterNACHI Field Guide for the Inspection of Wood Roofs (PDF)
InterNACHI Field Guide for the Inspection of Slate Roofs (PDF)
InterNACHI Roof Field Guide Total Package (PDFs)
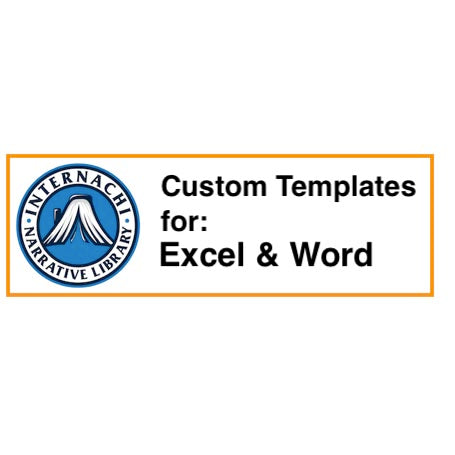